キールバルブの鋳造に入ります。やり方は前回U号と同様です。
まず、アルミホイルで鋳型を包みます。厚さは、4〜5周くらいです。シワを作った方が強度がでます。写真64
その上に、マスキングテープで補強します。写真65
ストラットを差し込む箇所と湯口とする箇所にマジックで印を入れます。写真66
湯口は、空気抜きも兼ねるので、一番高い所(今回は先端近く)としてます。
最大径の部分で輪切りにし、鋳型を抜きます。写真67
|
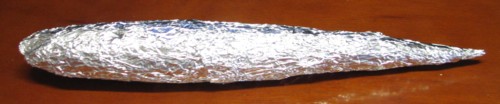
写真64 |
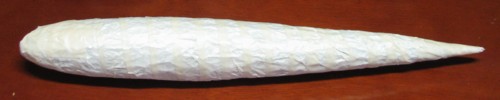
写真65 |

写真66 |
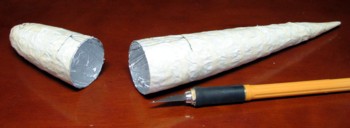
写真67 |
次に、ストラットを差し込む部位に、中子(なかご)を作ります。アルミホイルをストラット先端を包み、型どりします。差し込み深さ15mmくらいとしました。写真68
とった型を取付けます。写真69
そして、湯口を開けます。写真70
中子の厚さはアルミホイル2重と薄く、中空のままだとつぶれるし、砂が入っても破れるので、エポキシ接着剤を垂らして固めます。写真71
ガスコンロで加熱し、鉛を溶かします。前回のデータから、鉛は、1.6kgで約15分加熱しました。写真72
鋳込み用の箱が小さく、ぎりぎりでしたが、鋳込みます。・・・適当です。(~_~;)写真73
|
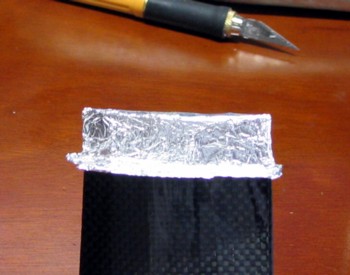
写真68 |
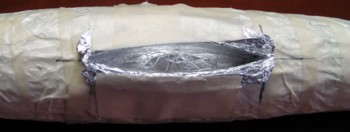
写真69 |
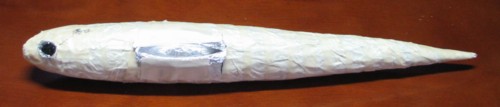
写真70 |
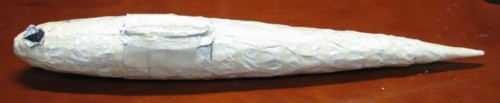
写真71 |
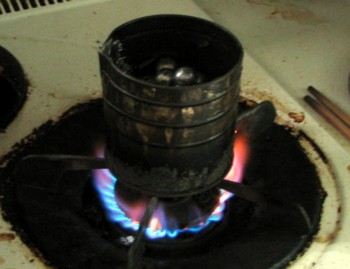
写真72 |
写真73 |
冷却放置2時間後に掘り出します。写真74
テープとアルミホイルを剥がします。鋳込み途中に、手元がブレて、湯口をふさいでしまったので、中断した跡が・・・(筋が入ってます(>_<)・・・パテで整形できるので良しとします。(^_^.))写真75
アルミホイル輪切り鋳造法の欠点
・シワがどうしてもできる。
・砂圧や手で持った力、鉛圧で、真円がくずれやすい。
湯口部周辺の拡大:ひけはどうしてもできます。写真76
■データ
バルブ重量1.45kg
鉛:追加購入分1kg/960円
累計6,448円
|
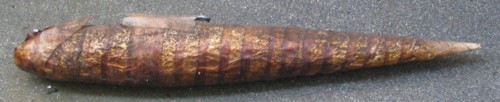 写真74 |

写真75 |
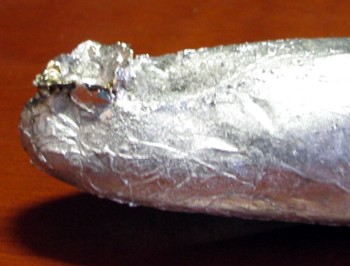
写真76 |